AI SERVICE PROVIDER
SERVICE
SERVICE OBJECTIVE
Ensure and protect productivity, reducing maintenance costs and unwanted downtime, constant effort in production improvements and generating Insights.

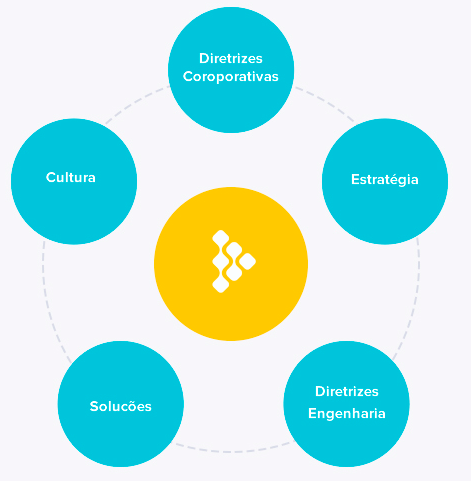
Solutions
Our developed solutions are always elaborated from larger objectives and institutional declarations of the company, being: Mission, vision and strategic corporate guidelines, marketing, commercial and customer relationship.
In an active way we will help to ensure the gains that the services offered by the division of DIPSIE SERVICE, fully fulfill its objectives while maintaining the “corporate strategic coherence” determined by our customers.
WHY IS THAT?
Maximize the utilization of existing systems, improving the quality of operation, generating cost reduction and integrating the information. (Increase in quality of life, sustainability, operational efficiency, cost reduction and EBITDA increase)
As?
Giving the vision of how to increase the utilization of the existing structure, understanding the concept of improvements that can be applied with low effort and investment but that cause large positive impacts throughout the operational chain.
WHAT’S THAT?
Solutions and technologies should be developed in order to leverage the existing infrastructure (hardware and software) in order to maximize its potential.

TRADITIONAL X DIPISIE SERVICE
Traditional model
of service Contracts
of technical assistance
The traditional models of maintenance contract, have high cost, because they create the link of emergency care, and often with dedicated people,
HIGH MAINTENANCE COST
Contract model
Maintenance
Dipsie Solution
The traditional maintenance contract models have a high cost, as they create the emergency service bond, and often with dedicated people.
MACHINE LEARNING AND MONITORING
REAL-TIME
OUR SYSTEM
Through our system, we do all the monitoring in real time. The X-Machine system covers all STAGES of maintenance, operation and Safe
PREDICTIVE MAINTENANCE
MACHINE LEARNING
This technique is based on the principle that long before it presents a failure, an industrial machine emits small signals of deviation, initially subtle and subsequently of greater amplitude, which can be used for a premature diagnosis of the failure . The practice consists in the sensorization of the assets making available the measurements for an industrial analytical system capable of monitoring the asset in real time, combining the variances between variables, doing diagnostics and passing them to the management platform of the Maintenance (X-Machine).
The Maintenance Planner now has access to a robust diagnostic tool that directs interventions to the assets that are really close to presenting a defect.
With microprocessed sensors that perform readings of several variables, your data is sent to a cloud server, received and processed through mathematical modelling with Machine Learning techniques, which generate the probability of failures in Machines and alerts in real time to the determined people. The platform increases the availability and service life index of the equipment, significantly reducing the costs of preventive maintenance and unwanted downtime and long and programmed high-cost maintenances.
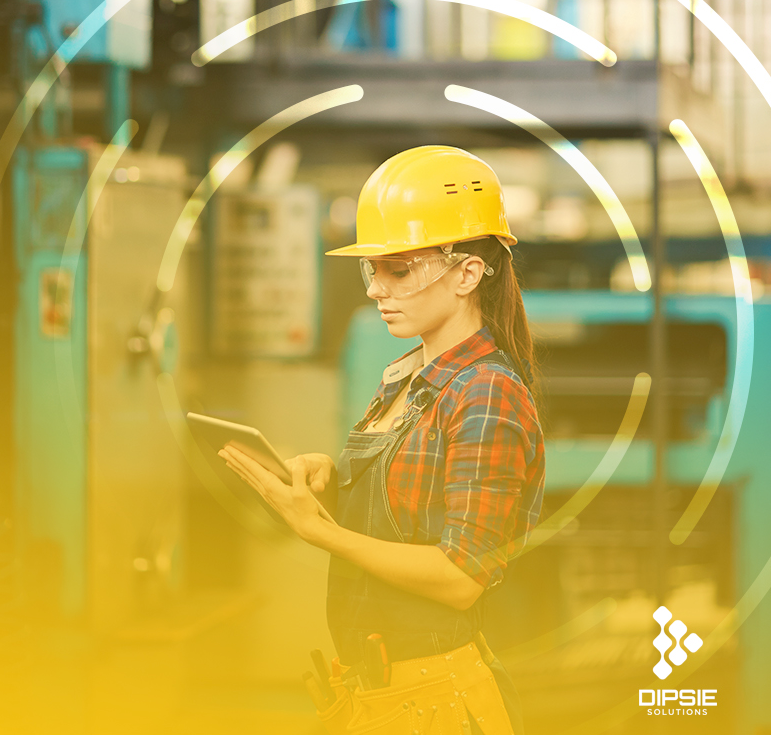
Differential
SOLUTIONS & SERVICES
Cost reduction
With maintenance
Reduction of maintenance costs, without the need for large stops, intervening before the problem happens, a significant increase to the sim of a semester.
Cost reduction
With Stop machine
Through an intelligent system that performs 24×7 monitoring, preventive actions are performed with punctuality and greater assertiveness, avoiding unwanted stops.
Assertive interventions
With expressive results
With online monitoring and access to systems, the support team will perform interventions optimizing costs of displacements, time or sending a specialist with all the information.
Assertive interventions
With expressive results
With online monitoring and access to systems, the support team will perform interventions optimizing costs of displacements, time or sending a specialist with all the information.
SUCESS FEE
We are open to negotiate remuneration models contemplating “Sucess Fees”, or any other non-conventional model, assuming with our partners the commitment to deliver the proposed benefits. In other words…
Dipsie Solutions puts your (commitment) on the line!
